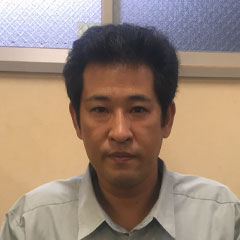
代表取締役社長 渡邉和彦
● はじめに
弊社は、切れ味が衰えた工具の再研磨による再生や、壊れた工具の一部から工具を再製作すること、それらのノウハウから工具を新規製作するという3本柱にした研磨業に携わる企業です。わかりやすく言えば、エンドミルやドリルなどの切削工具の「改造もできる修理屋さん」です。
● 入社まで
昭和62年に父である会長が設立し、平成26年8月から私がこの会社の舵をとることになりました。私が中学生のときには研磨の仕事自体は父が既に始めており、父は「家族で仕事をやってこう」と早くから私たちに聞かせていました。しかし、そのときには父と同じ道を行くことになるとは考えてもみませんでした。工業高校に進んで工業について勉強してゆくうちに、父とこの会社を営んでいく決意が固まってゆきました。卒業も間近で会社設立の目途もたったころ、「3年間から10年は他所で働き揉まれてこい」と父に言われました。仕方なく、私は興味が一番あった金型メーカーに勤めることを決め、切削工具を用いた加工に4年従事しました。そこでは、切削工具のユーザーとして、「造り手」にはない「使い手」の視点を養いましたが、一番の収穫はなんといっても、数値制御加工機のオペレーターとして勤めた経験にあると思います。この経験が今の会社運営にとてつもない影響を与えたのですから。
● 入社当時の研磨と課題
私が入社したのは24年前、平成4年の3月ごろのことでした。当時の再研磨といえば、汎用機でカケを取るだけでいいような依頼が多数でした。しかし、機械、刃物、コーティングなど切削工具を取り巻く技術の進化は目覚ましく、弊社の再研磨品に求められるレベルも新品同様になるまでにそう時間は掛かりませんでした。これらを解決していくにあたって、様々な課題が発生しました。例えば、外径寸法、C面、コーナーR、ボール部R、真円度、芯圧、フレ、スクイ角、刃角、ネジレ角などの要素の精度をいかに研磨で向上させるのか?そして、これらを満たす工具を研磨できるオペレーターを増やすには? 精度をクリアーしたとしても、その精度をいかに保証するか?製造課長として現場を指揮することになると、私は課題解決のため数多くの取組を行いました。
● 砥石成型へのこだわり
私のこだわりのひとつとなった取組として、砥石の微細なフレの除去を徹底して行わせ、鏡面仕上げが出来る精度を常に維持するようにしたことが挙げられます。工具を研磨する機械はどんな場合でも、砥石を用います。砥石の精度は研磨の精度、そして切削工具の精度と切削性能に直結するのです。包丁などの刃物も荒い砥石で大まかに研いだあと、目が細かい砥石で研ぐとよく切れるようになりますが、それと同じことです。こうした取組を通して、「もしかしたら新品以上かもわからんぞ!」とお客さまにも大変喜んでいただけるようになったという経験は、私の自信の源となりました。平成19年にはKIRNER社製砥石成型機「K-42」を導入し、この取組をより高度に洗練して行うことを可能にしました。この取組は今後も徹底していき、より洗練させ、向上させていきます。
● 客観的な検査・測定の必要性
また、私の入社後4年ほどの間に、弊社では国内のトップメーカーの再研磨の代行なども積極的に行うことでノウハウのいっそうの蓄積に力を入れることになりました。メーカーの研磨品には厳格な精度が求められますが、投影機や顕微鏡を用いた検査・測定で精度がきちんと出せていることを示し、メーカーも了承して下さいました。しかし、メーカーからの依頼が増え、精度の添付を求めるお客さまも徐々に増えるにつれて、客観的に精度を保証し、お客さまに安心して工具を使用してもらう必要を私は強く感じるようになりました。平成21年にZOLLER社製CNC測定機「Venturion-450」を導入し、測定・検査の客観性を確保しました。今年(平成28年)6月にはKEYENCE社製デジタルマイクロスコープ「VHX-5000」を導入し、ドリルなど先端頭頂からの測定を可能にするなどより高度な検査・測定を行える環境を整えるなど、弊社ではより優れた精度で加工し、それを示し続けることでお客さまの信頼に応えていきます。
● 研磨・製造の問題
加工面での問題として印象深いのは、私の入社後に需要が増してきていたボール形状やラジアス形状などのエンドミルを主とした工具の精度についてでした。ボールエンドミルなどの研磨では、汎用機でR精度を交差に入れるのは容易ではなく、これには、創業当時の前社長(現会長)もなかなか手を焼いたようです。そのため、これらを研磨できるまでにオペレーターを育てるのには時間が掛かります。前社長(現会長)や私たちを含めた一部のオペレーターのみで研磨を行い、並行して後続のオペレーターを育成することにしました。しかし、メーカーからはより高度な切削工具の依頼もどんどん増え、研磨に追われ後続のオペレーターを育成する余裕がなかなか取れない状況がすぐに訪れ、当初の目論見はすぐに頓挫しました。
● 工場のNC化の決定
状況を打破すべく、生産技術課長(現専務)とともにCNC工具研削盤の導入の必要性を社長(現会長)に訴えました。私と専務はともに別々の金型メーカーに勤め、マシニングに触れていました。つまり、「数値制御=NC(Numerical Control)」の有益さを早くから、身を持って体験していたため、研磨業界においても「コンピューター数値制御=CNC(Computer Numerical Control)」が有用であると確信することができたのです。平成9年から13年までの4年間に段階的に研削プログラム「MSPS」により自動に正確な加工ができる牧野製高精度CNC工具研削盤「CNJ2」6台を主力とした安定した研磨体制を整えました。なにより、経験が浅いオペレーターでも、作成したプログラムどおりに操作すれば、比較的容易に精度が出せるうえ、何本もの工具を同形状に安定させられるという点が画期的でした。こうして、効率的な体制へと移行することで、生産能力の底上げと同時に、次世代のオペレーターを育成する時間も徐々に取ることができるようになりました。
● さらなるNC化の促進
加えて、平成20年から26年には同じく牧野製で新研削プログラム「MSPSⅡ」が搭載された改良型CNC工具研削盤「CNJ2u」4台を追加し、スローアウェイチップなど再研磨や、より複雑な製作へも対応しました。「CNJ2u」は旧研削プログラム「MSPS」での研削に対応しています。なので、この4台の新しい機械を6台の旧い機械に合わせることで、まったく同条件で同じものを一定の規格どおりに大量研磨するという使い方も可能であることが決め手となりました。6台規模のラインと新型4台規模のラインの2つという状態と、10台規模のラインを1つという状態を臨機応変に選択できるのが弊社の強みとなりました。道程はとても長いものでしたが、こうして弊社の研磨許容能力は格段に向上し、仕上げ加工用工具の再研磨を弊社で行うことは当たり前の光景となりました。
● 結び
このように、社長として舵を取るようになって日の浅い身ではありますが、社員時代より節目で大きな役割を果たしてきたと自負しております。また今回、社長として初めて、今年中にさらに加工の幅が広い上位機種を導入することを決めました。私たちがここまで課題を乗り越え、歩んでこられたのは、一重に日ごろからの皆さまの支えがあってこそだと思ってきました。社長となった今、過去において皆さまの支えがいかに大きなものであったのかをよりいっそう痛感しております。これからも現状に満足する事なく、引き続き匠な技術を、心を籠めてお客さまにご提供し、技を磨き続けますので、この先もいっそうのお引き立てのほどをお願い申し上げます。
渡邉和彦(平成28年8月)